Understanding Chlorinated Solvents in Site Assessments
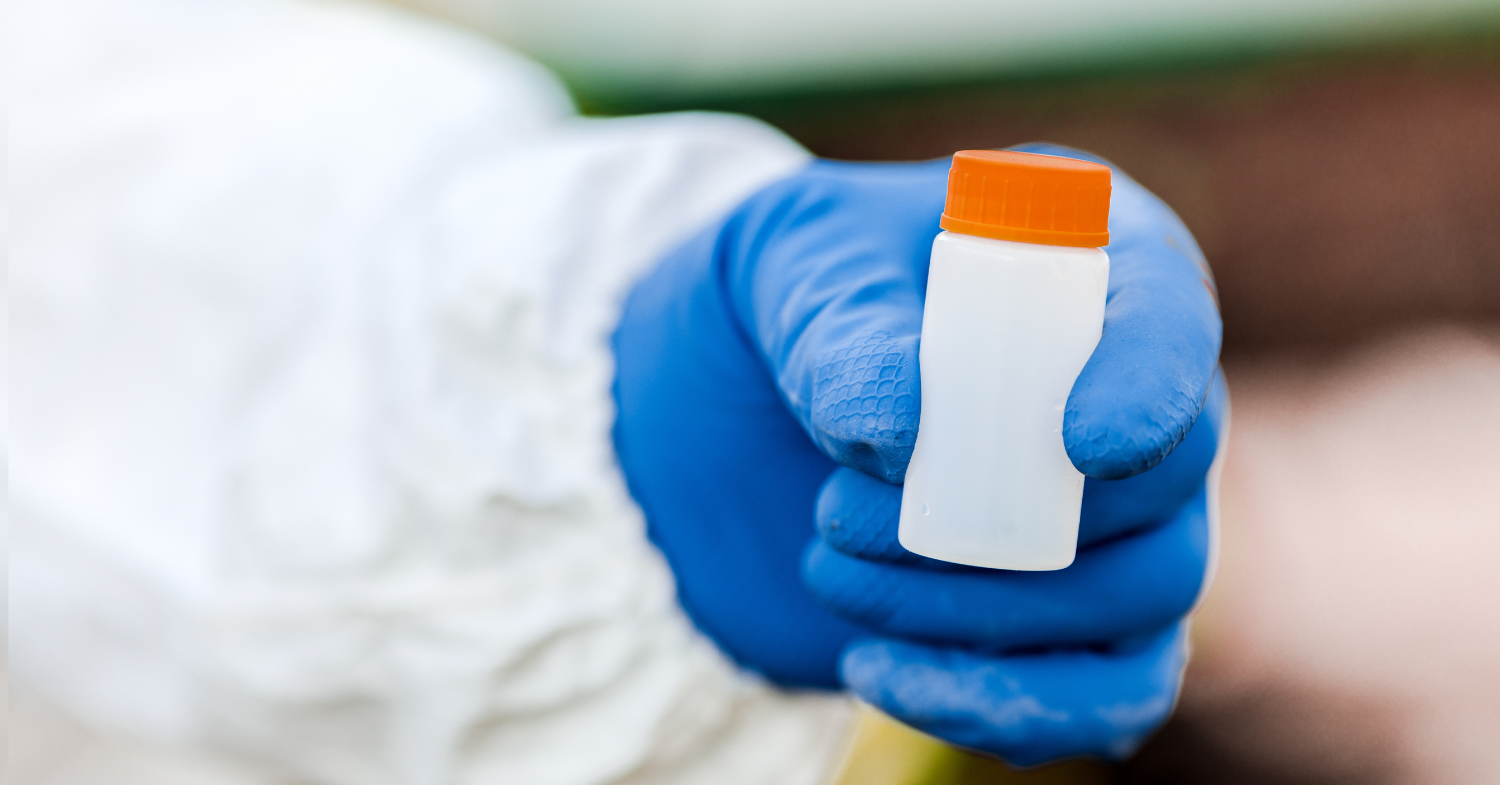
Chlorinated solvents, commonly used in various industrial and commercial applications, present significant environmental challenges during site assessments. These compounds can be a concern for real estate developers, regulatory agencies, and environmental consultants alike.
Blog Highlights
In this blog, we’ll dive into what chlorinated solvents are, their implications for environmental assessments, how they impact redevelopment projects, and how APEC can help mitigate associated risks and control costs.
What Are Chlorinated Solvents?
“A chlorinated solvent is a chemical compound that consists of one or two carbon atoms and at least one chlorine atom joined by covalent bonds” [1]. Chlorinated solvent compounds are listed as a volatile organic compound (VOC) and can easily migrate into soil and groundwater.
Examples of some chlorinated solvent compounds include:
- Tetrachloroethene (PCE) aka PERC
- Trichloroethene or Trichloroethylene (TCE)
- Dichloroethene (DCE)
- Vinyl chloride (VC) [2].
Their persistence and mobility in the environment make chlorinated solvent contamination particularly concerning for development projects. Due to the toxicity of chlorinated solvents, long-term environmental and health risks can occur if not addressed properly.
Chlorinated Solvent Contamination in Site Assessments
When conducting a Phase I Environmental Site Assessment (ESA) or Phase II Subsurface Investigation (Phase II), identifying the potential for chlorinated solvent contamination is a critical step. A Phase I ESA focuses on the property’s history and potential sources of contamination (onsite or offsite), while a Phase II involves sampling of soil, water, or air to determine if these chemicals are present [3].
Chlorinated solvents are often found in areas with industrial or commercial use, especially in properties associated with dry cleaning, manufacturing, chemical production, or automotive services. If contamination is suspected, it is essential to assess the presence of or the extent of chlorinated solvent migration to prevent future complications.
Impact of Chlorinated Solvents on Environmental and Real Estate Projects
The presence of chlorinated solvents in a site assessment can have significant repercussions for real estate transactions or development projects. These chemicals can spread far beyond the site’s property boundaries, creating large contamination plumes. Failure to assess and address this contamination can lead to long-term liability issues, expensive remediation, and regulatory penalties.
For real estate developers, chlorinated solvent contamination can add complexity to the redevelopment process. Properties impacted by these chemicals may require extensive cleanup before they can be redeveloped, increasing costs and extending project timelines. Potential buyers or investors may also hesitate from property transactions due to the risks and potential liabilities associated with these contaminants.
APEC Can Help Mitigate Chlorinated Solvent Risks & Cleanup Costs
It is vital to not only conduct site assessments to confirm the presence of volatile organic compounds like chlorinated solvents, but ensure such assessments are executed properly. At APEC, we specialize in providing comprehensive site assessments and remediation services, particularly for properties affected by chlorinated solvents. Our team utilizes both ASTM Standard E-1527-13 and ASTM Standard E-1903-11 to identify the extent of contamination, ensuring that environmental risks are addressed efficiently and cost-effectively.
By partnering with APEC, real estate developers and investors can confidently navigate the challenges posed by chlorinated solvents. APEC can also help mitigate the costs of chlorinated solvent remediation projects by finding creative ways to help pay for these cleanups. APEC also has extensive experience working with state regulatory agencies to handle chlorinated solvent contamination by effectively applying risk-based methods of closure. Our team of professional geologist, engineers, and hazardous materials managers are committed to helping clients ensure regulatory compliance, protect public health, and streamline their development efforts.
APEC is a developer friendly business that understands risk and liability. We will work with developers and investors to make sure their development projects keep moving forward without the high risk and cost of dealing with chlorinated solvent contamination.
References
- American Concrete Institute. (2021). Specifications for Concrete Construction (ACI 301-20).
- International Concrete Repair Institute. (2013). Guideline for Surface Preparation for the Repair of Deteriorated Concrete Resulting from Reinforcing Steel Corrosion (ICRI 310.1R-2008).
- National Institute of Standards and Technology. (2013). Improving Concrete Bridge Decks with Internal Curing.